A DEFINITION OF CUTTING
Down at the level where the edge meets individual wood fibers, cutting is synonymous with breaking. The point of the tool presses against the wood fibers with enough force that they break, separating into two pieces. A cutting edge concentrates all the force driving the tool at its point. And because a sharp edge contacts only a small amount of the wood surface, the resistance is confined to a tiny area. The keener the point, the smaller the resistance, and the smaller the force required to cut. The wood fibers separate along a narrow line described by the path of the tool, and the cut surface appears smooth and even. A blunt or dull tool contacts a larger surface area. Consequently, there is more resistance and it requires more force to cut. The fibers fail along a wider, poorly defined line, and the cut is ragged.
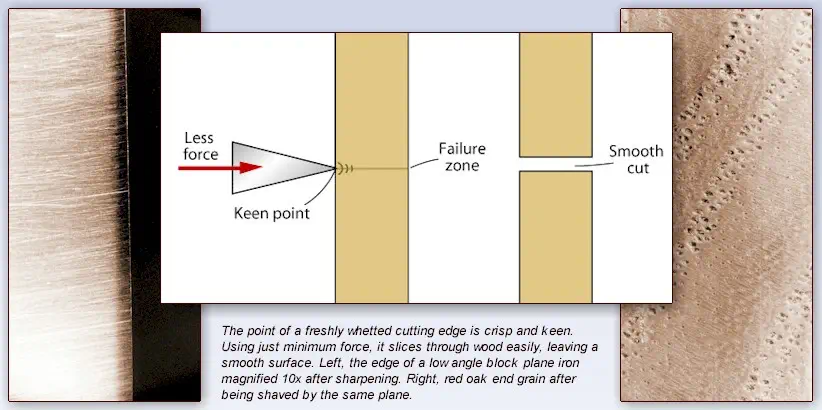
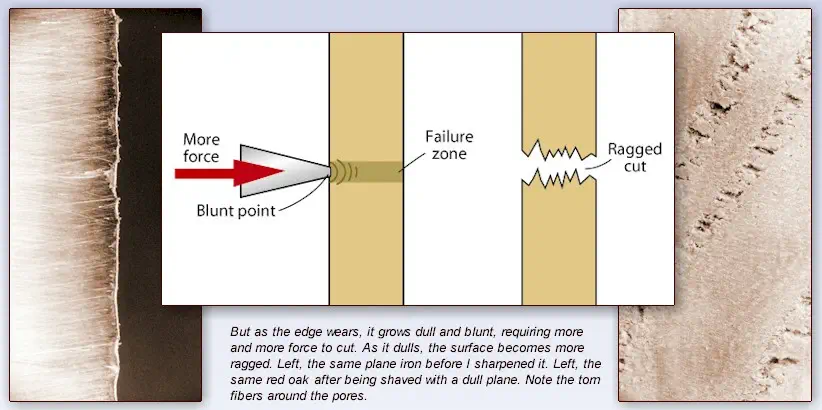